INDUSTRIAL DESIGN
W I N G S
May 2019
WINGS is a spinal support solution for first response aquantic rescue use that is easy-to-use, time saving, effective at immobilizing patients, versatile across a wide range of trauma situations and body types and durable.
​
This is a collaborative project with RISD, MIT Engineering School and MIT Sloan School of Management, in the Product Design and Development Studio.
​
Design in collaboration with Audrey Bazerghi, Marcus Chao, Jana Saadi, Souhail Salty, Ellen O’Connell.
​

01 /CONTEXT


PROBLEM STATEMENT
Spinal board is a vital equipment for aquatic rescue, however remains to be developed. Our team conducted quite a few interviews with a variety of stakeholders that had been involved in the use of spinal boards across markets (e.g., ground EMTs, lifeguards, injured patients that had been put on a spinal board). Ultimately, after deciding to narrow our focus towards aquatic uses of spinal boards we conducted additional even more in depth interviews with the lifeguards who are the primary users of the spinal boards.
​
We’re largely convinced that there are considerable opportunities in the aquatic applications of spinal boards (particularly for pool lifeguards). We find that lifeguards experience quite a few pain points in using a product that hasn’t been improved upon for a long time, and they represent quite a sizeable market opportunity.
Interviewing lifeguard at MIT Zesiger Sports and Fitness Center.
USER JOURNEY


After understanding lifeguard’s pain points through interview and observing the user journey, we were able to synthesize the following aggregate primary needs:​
​
-
Speed of deployment: Can the product be moved and deployed quickly both in and out of the water?
-
Ease of deployment: Can the product be deployed with the patient using a relatively small number of easy steps, and few lifeguards?
-
Control of board positioning: Can the product be effectively manipulated and controlled to accurately be positioned under the patient?
-
Immobilization: Can the board effectively immobilize the patient to avoid further injury?
-
Body-type versatility: Can the product support patients of diverse body-type And be comfortable?
Brainstorming based on the ‘user journey’. Organized in the decomposed user steps: carrying, in, on, immobilize, out, maintenance.
COMPETITIVE ANALYSIS
Based on our competitive analysis, we’ve concluded that the boards in the market today offer a wider variety for non-aquatic applications and tend to rely on complicated strapping mechanisms that the user does not prioritize. We believe the potential market is promising for our design.

Table 1. Competitive analysis of 4 existing products.
02 /CONCEPT GENERATION
IDEATION

/ SKETCH
Brainstorming session and sketch ideas.
/ EXPERIMENT

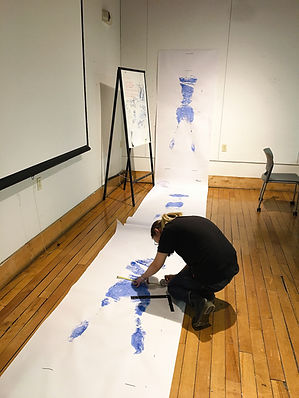
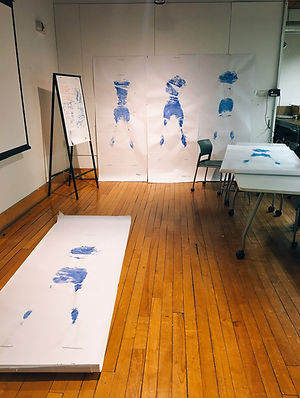
Body Length Measurement and Data Collection

Different uses of the work-like extendable mechanism of the board

Two methods tested to inflate a balloon underwater, handpump (left) and compressed air can (right)
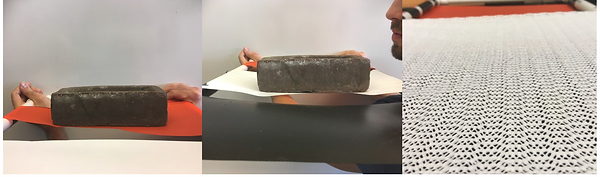
Different materials for their respective deformations under an applied weight
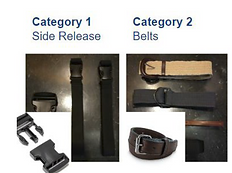
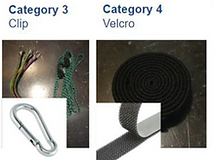

Testing different types of strapping mechanisms
CONCEPT EVALUATION
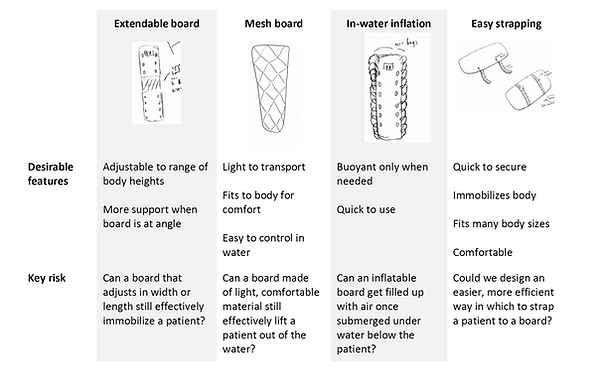

-
Develop a solution with variable buoyancy: an inflation mechanism that provides buoyancy only when needed to achieve speed and ease of deployment for the board.
-
Revisit board composition: as the board does not need to be buoyant itself anymore (the inflation solution will take care of that), its shape and materials could be optimized to be lighter and easy to maneuver.
/ KEY DECISIONS
03
/DESIGN DEVELOPMENT
/ FORM & SHAPE REDESIGN
In order to design the shape of the board, I modeled small scale board shapes using blue foam. These boards differ in terms of shape, curvature, hole locations and edges. I then tested these boards in water by submerging the boards underwater at different angles and observing the orientation at which they floated up, how quickly they did as well as how evenly. The results of the testing are outlined in the table.


From testing we determined that the optimal board shape is an oval that is curved on the (concave) on the bottom surface, has symmetric holes on the head and leg locations, and has edges on the side. With this design we are able to easily submerge the board at a 90 degrees or less and ensure that it raises smoothly to life the patient out of the water the right side up.
/ INFLATION

We decided to use inflation under the board to allow us to vary the buoyancy once it is in the water. This would allow the lifeguards to easily submerge and maneuver a low buoyancy board under the patient, and then within seconds inflate the board to lift the patient above the water. From our quick testing with CO2 cartridges we learned that inflation under water is doable, however the cartridges themselves were too small to inflate to the full volume we needed. Therefore, we chose to use a refillable, high pressure air (HPA) canister, traditionally used for paintball guns.
/ FINAL PRODUCT SKETCH

/ FINAL PRODUCT CAD MODEL

Assembly CAD model
Detail of winged shape
Detail of pneumatic system
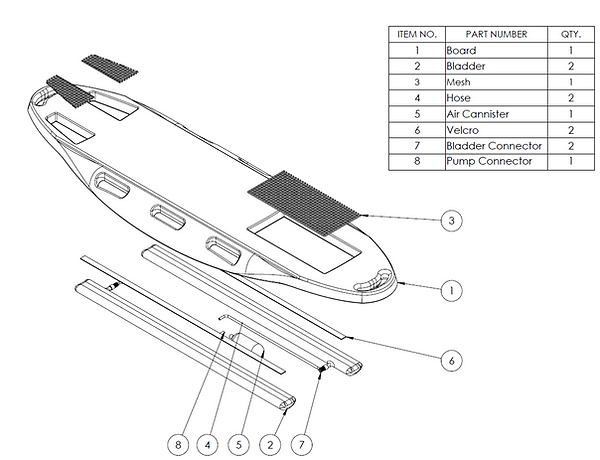

04
/PROTOTYPING & TESTING
/ PROTOTYPING PROCESS



/ FEATURES







/ PROCESS &TESTING
DOCUMENTATION
